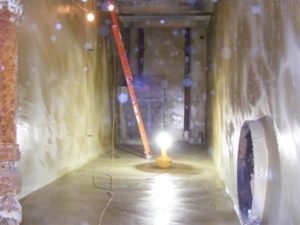
Case Study:
Michelin US1 Plant
Client
Michelin Plant in Greenville, South Carolina
Problem
The work needed to be done over the Christmas holiday shutdown, and neither of the structures to be rehabilitated could be taken out of service for pre-bid inspections.
Solution
8,000 sq. ft. of the surface of the cracked wall needed to be parged by hand trowel to bring the wall up to spec. Then, SprayWall® could be applied to the structure, from 150 to 250 mils. thick in some places.
MICHELIN US1 PLANT
Industrial plant cooling tanks get a new lease on life for Christmas
Situation:
The phrase “driving with your headlights off” comes to mind when referring to this project. The Michelin Plant in Greenville, South Carolina, had a substantial infrastructure issue that required rehabilitation. The only problem was that the work needed to be done over the Christmas holiday shutdown, and neither of the structures to be rehabilitated could be taken out of service for pre-bid inspections.
The project consisted of two (2) below-grade, concrete, closed-top cooling tanks. The 10,000 sq. ft. total surface area was accessible only through two 20′ manhole entries per tank. The scope of work included the removal of existing 23-year-old liner material and the installation of SprayWall® by Sprayroq at 100 mils. throughout the structure.
Solution:
When you go in blind, you can only expect the worst. To learn what they were really up against, our certified SprayWall® applicator needed to remove the existing tank liner. This would allow them to find out how bad the structure underneath had deteriorated.
After the existing liner was removed, workers found that due to numerous cracks, water infiltration was much more severe than anticipated. Our team dealt with this problem by injecting 500 linear feet of floor-to-wall cold joint, and an additional 200 ft. in the wall cracks. This allowed the our Sprayroq crew to begin pressure-washing the structure. It was at this point when it was determined that 8,000 sq. ft. of the wall surface needed to be parged by hand trowel to bring the wall up to spec. After all this preparation was complete, SprayWall® could be applied to the structure, from 150 to 250 mils. thick in some places.
Results:
On New Year’s Eve, the scaffolding was lifted out of the hole by a rope through one of the 20′ manholes, as the last of the SprayWall® was being applied. The project was completed on time, with no lost production for the plant.
Request a Free Sample
Want to test out the product for yourself? Reach out to us today and we’ll send you a sample of our product so that you can see for yourself all the great things that trenchless technologies can do for you and your business.
Learn More Today
Interested in finding a Sprayroq™ Certified Contractor in your area? Have questions about our products? Click the button below to contact us and one of our team members will reach out as soon as possible.
Apply to be a Sprayroq™ Certified Partner
Apply to become a Sprayroq™ Certified Partner (SCP) and you too can experience the profitability that comes with protected territories and a powerful, resilient product that you can trust.